Meet Associate Professor Jeremy Hobbins, the man behind the BA (Hons) Horology course at Birmingham City University, which is helping to shape the next generation of watchmakers
British horology is undergoing a renaissance, with micro-brands popping up around the country, larger companies like Christopher Ward competing – and beating – the most esteemed names in watchmaking, and the new Alliance of British Watch and Clockmakers proving to be a unifying voice for the industry.
One of the key drivers for people looking to get into watchmaking is the BA (Hons) Horology course at Birmingham City University. Here, course head, Professor Jeremy Hobbins, tells us how the degree prepares his students for a career in watchmaking – and why he still considers himself a ‘fixer’.
Hi Jeremy. How did you become a horologist?
The horology course I studied in the 1990s followed the distance learning course of the British Horological Institute. But during my time as a student, the university created its own HND [a qualification] pathway. That ran alongside the BHI course. When I was brought back here to lead the BHI pathway, my former lecturer was still here, but he took early redundancy and I took over the whole provision. For a number of reasons, having both a further education course (BHI) and a higher-level course (HND) running side by side was complicated, so we united everything into a degree format.
I consulted with the industry to make sure the course had everything it needed and the right academic outcomes to qualify as a degree status. We launched it in 2012 and it’s been growing ever since.
What type of students do you attract?
The average age is in the early 20s. The majority have thought deeply about what they want to do because it’s so expensive to be a student. Most are drawn by the glitzy world of watches – around 70 percent – though a small cohort are drawn to clocks, too. We have the occasional student who comes here to indulge themselves: some see themselves as the next George Daniels or Roger Smith, and think it’ll be relatively easy to design and build their own watches. They find that’s not always the case!
What are the key skills you teach?
There’s a difference between teaching, and training, somebody. We’re developing the flexibility of individuals to shape their own career path. I give my students the ability to project-manage, plan, research, work in groups (or alone), and to present themselves and their work across a variety of mediums. At the same time, they also pick up a strong knowledge of horological mechanisms: how they work, how they’ve evolved, what are the most common faults – and how to rectify them. In year one, we teach them an engineering CAD program called Solidworks, which CW’s designers will be familiar with. We show how that software can also be used to control manufacturing equipment.
Tell us about the link between the course and Christopher Ward…
We first met at Salon QP [a watch show] in 2014, and they’ve supported us ever since. Today, CW sponsors a prize on horological movement design for our second-year students. That’s based around two strands: one, working together in groups to design a clock for public space; and second; working solo on a mechanism of their own. In the third year, they actually make the clock.
”Students get good by spending a lot of time at the bench“
So traditional skills are vital…
Of course. We concentrate on the practical elements of service, repair and restoring horological mechanisms. A significant part of the course is about those fine hand skills, so students can make bespoke components themselves, but also finish components made by others. In high-end mechanisms, parts are often machine-made, then hand-finished to enable the components to work together. They may also be decorated by hand.
We also encourage students to look at other elements of industry, like business.We ask them what it would be like to set up and run their own business. How would they promote it? Where would it be sited? How would they work out their financial viability? It’s a broad approach compared to the Swiss way. We find our graduates move to an organisation and move rapidly up to management as they have these additional skills.
What else is Christopher Ward involved with at BCU? Mike France can see a need in the market for new designers. That’s a new area for us. Before we’d concentrated on how things work, but now we’ll be expanding the design side of things. The course is always evolving!
What sort of jobs do your graduates go for, and get?
I’m very confident about the employability of my students. When they’re good they’re attractive to employers. I know this because they get jobs quickly. We signpost them to the fact it’s a tough world and they need to demonstrate their skills. And they only get good by spending a lot of time at the bench.
The majority of last year’s cohort signed to employers within three or four days of finishing the course. Going on to work with people like Rolex, Richemont in the Cartier workshops, LVMH in Manchester and even William Oak at Christopher Ward!
Why do you still love horology? I’m a fixer, I enjoy making things work – whether it’s a mechanism or a group of people. What drew me to horology was the ‘fairy tale’ that I’d be the next expert on the Antiques Roadshow – a person who could handle things that have been through the generations. I got into education because I became interested in sharing my knowledge. I love it, especially the ‘lightbulb’ moment when a student really understands what you’re trying to get them to do.
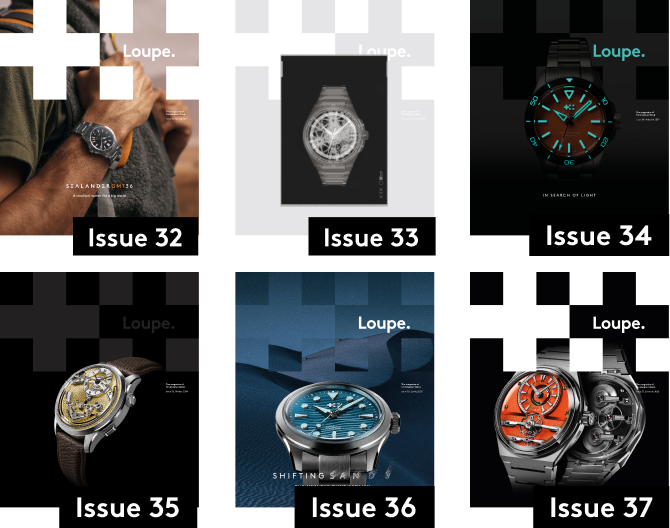
Sign up to Loupe magazine
Loupe is Christopher Ward’s quarterly in-house magazine. If you want to know what’s happening at CW (and you love great journalism), this is where to start. Alternatively, you can read all our back issues on your computer, tablet or phone.
Order your free copyRead Loupe online